ON-GOING PROJECT
Team & Project definition
A Boston University Masters in Social Work student, Ben Levine, and I are working on a BU Pardee Center for the Study of the Longer-Range Future fellowship project investigating the efficacy of using digitally constructed modular units in under-utilized spaces as a means of increasing affordable housing stock.
Role
Ben is working on the majority of research, including on the current state of and areas of opportunity in affordable housing in different cities around the country. My focus is on construction methodology, unit design, and financial modeling based on his research.
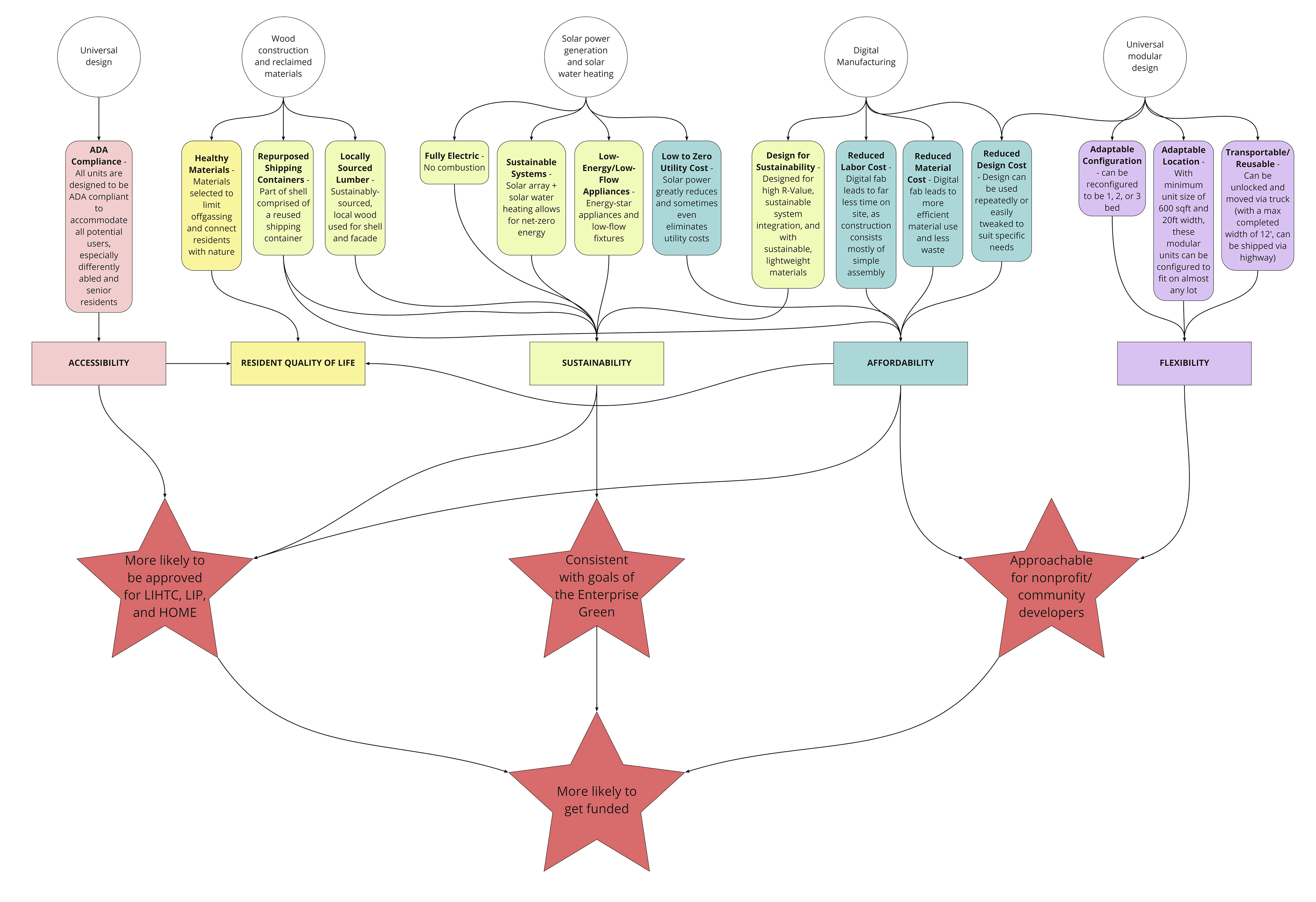
Research & DESIGN CONSTRAINTS
Our design constraints were largely defined by requirements and suggestions made in several different guidelines, including the MA Low Income Housing Tax Credit Qualified Allocation Plan 2022-3 (LIHTC), the MA State Building Code, the MA Smart Growth Zoning Act, the MA Local Initiatives Program (LIP), the US Department of Housing and Urban Development Affordable Housing and Multi-Family Unit Guidelines, and the US Department of Housing and Urban Development HOME Investment Partnership Program. However, we also wanted to ensure that our units would be 1) comfortable and accessible for any potential occupant and 2) affordable to develop at any scale so as to be attractive to nonprofit and community developers. Above you can find the map of how our design decisions (circles at the top) led to accomplishing primary, secondary, and tertiary goals.
cONSTRUCTION & UNIT DESIGN
The design and fabrication of these units is inspired by a British company called Facit Homes. Facit uses digital design and CNC fabrication to create the shell of their homes out of Lego-like CNC boxes. The process is incredibly efficient in terms of time, human resources, and material use, and the digital fabrication is done entirely on-site. Using this design methodology, we designed modular units that work for both on-site construction as well as factory fabrication, so as to allow for maximal flexibility. Each unit is comprised of 3-6 modular components, a mix of Facit-constructed wooden shells and high-cube shipping containers (so as to cut down on cost even further). All bathrooms and non-master bedrooms are located in shipping container components, and all master and communal living spaces are located in Facit-shell components. This allows for ADA compliance in all master bedrooms, communal living spaces, and bathrooms (to fit all necessary furnishings into the former two rooms, width beyond that of a shipping container is necessary, but an ADA bathroom can be designed to fit in a container). See below for floor plans and renderings of the 1-bedroom (left, top and bottom), 2-bedroom (center, top and bottom), and a case study development of our units on a city-owned lot in Boston (right).
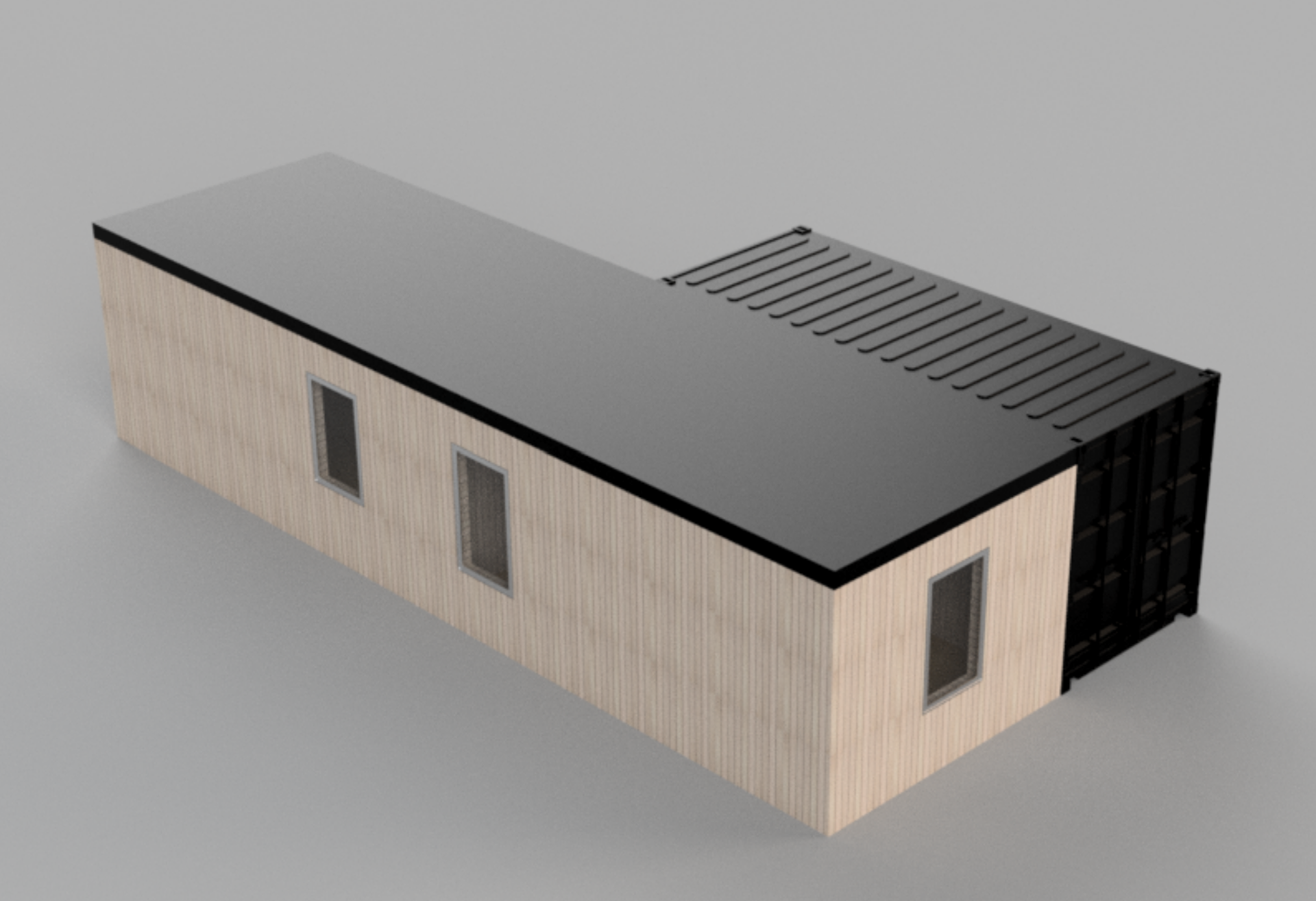
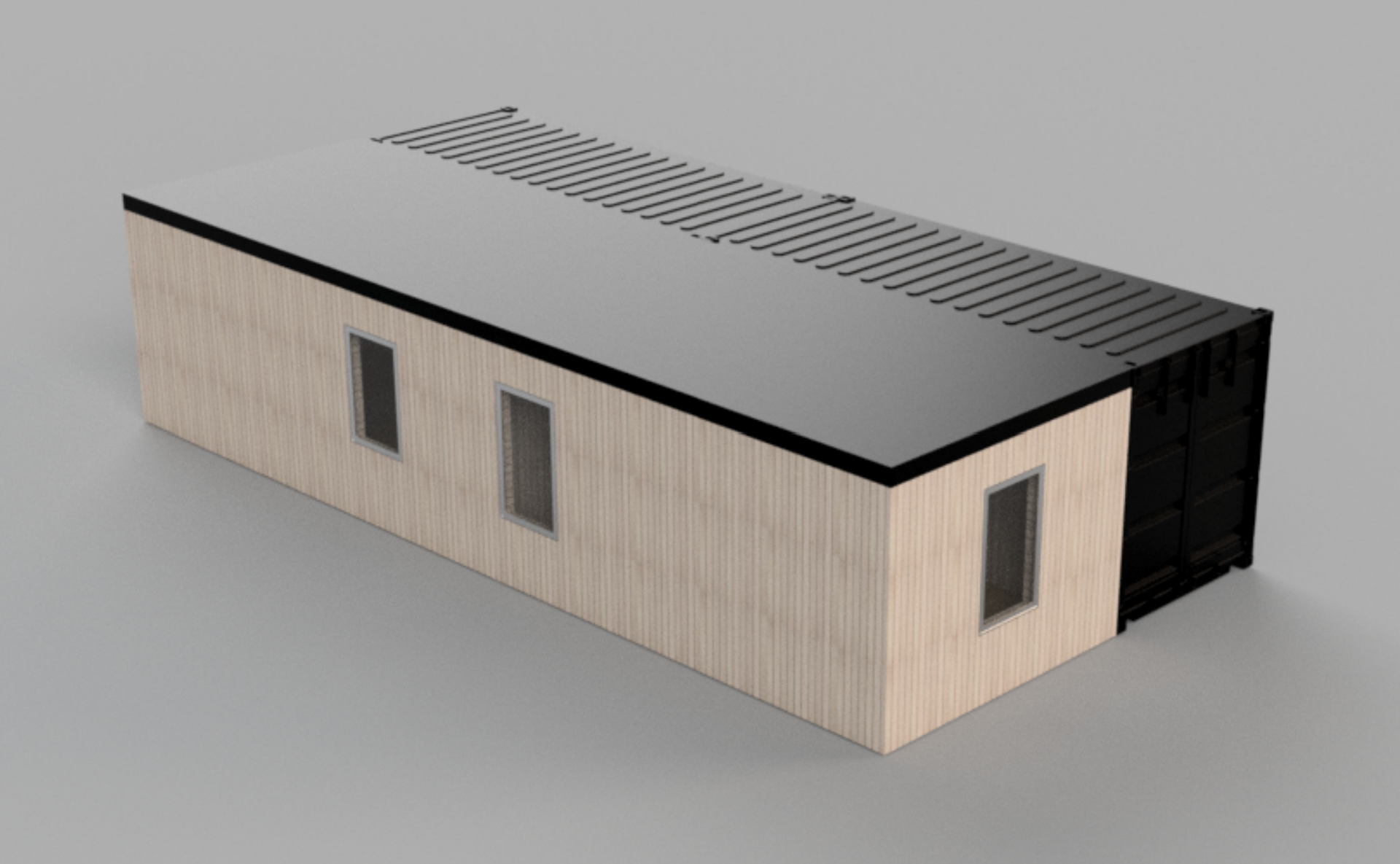
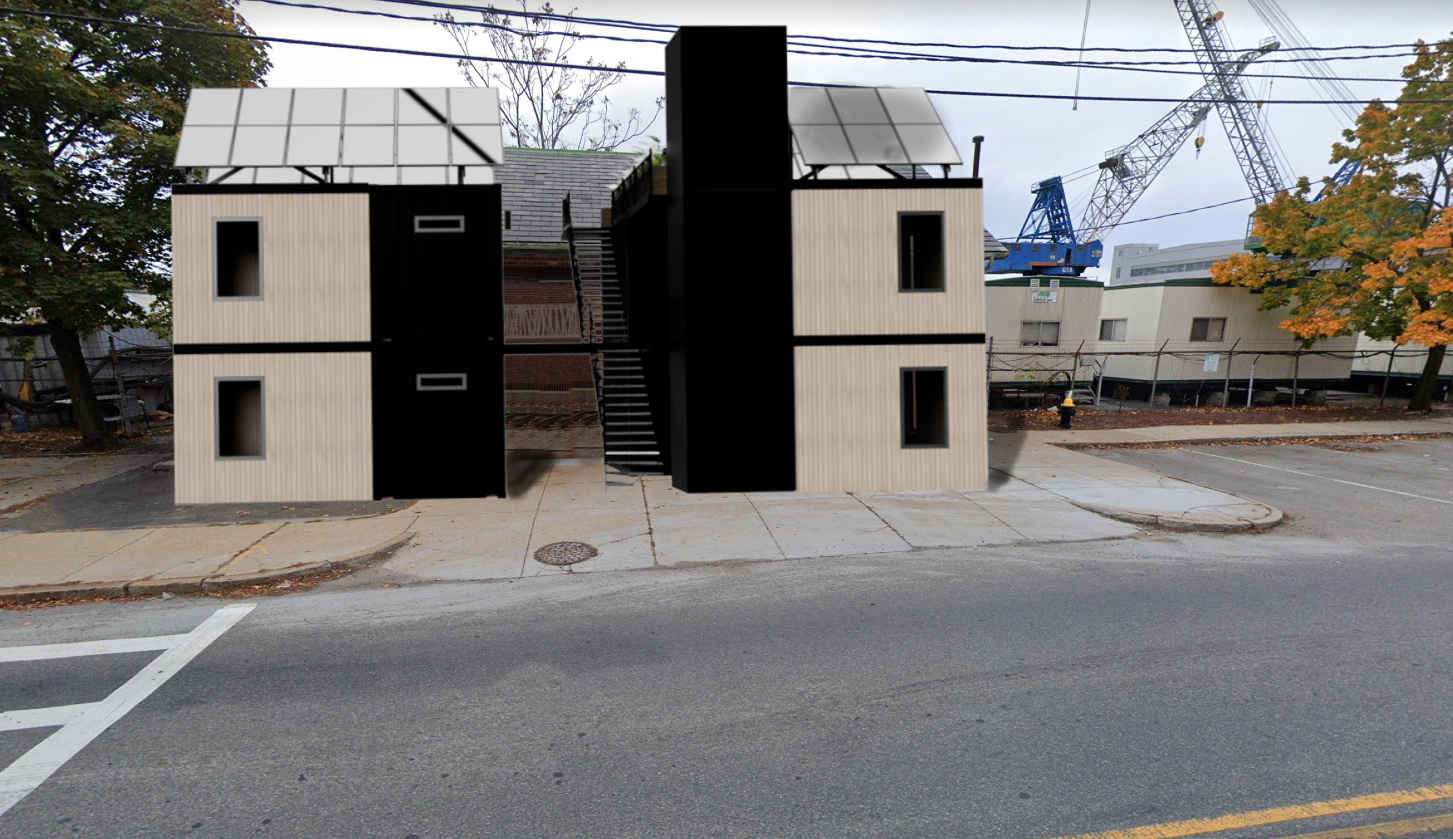
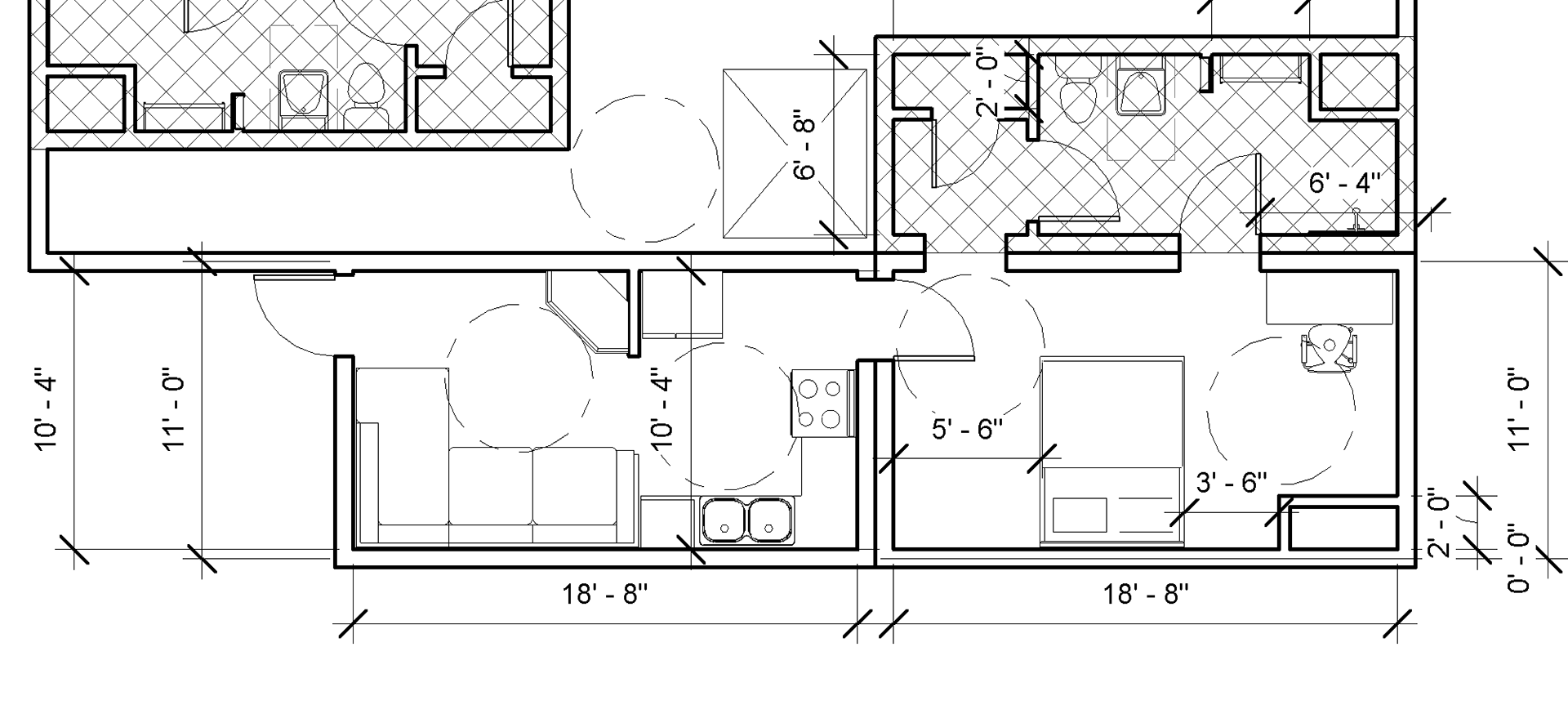
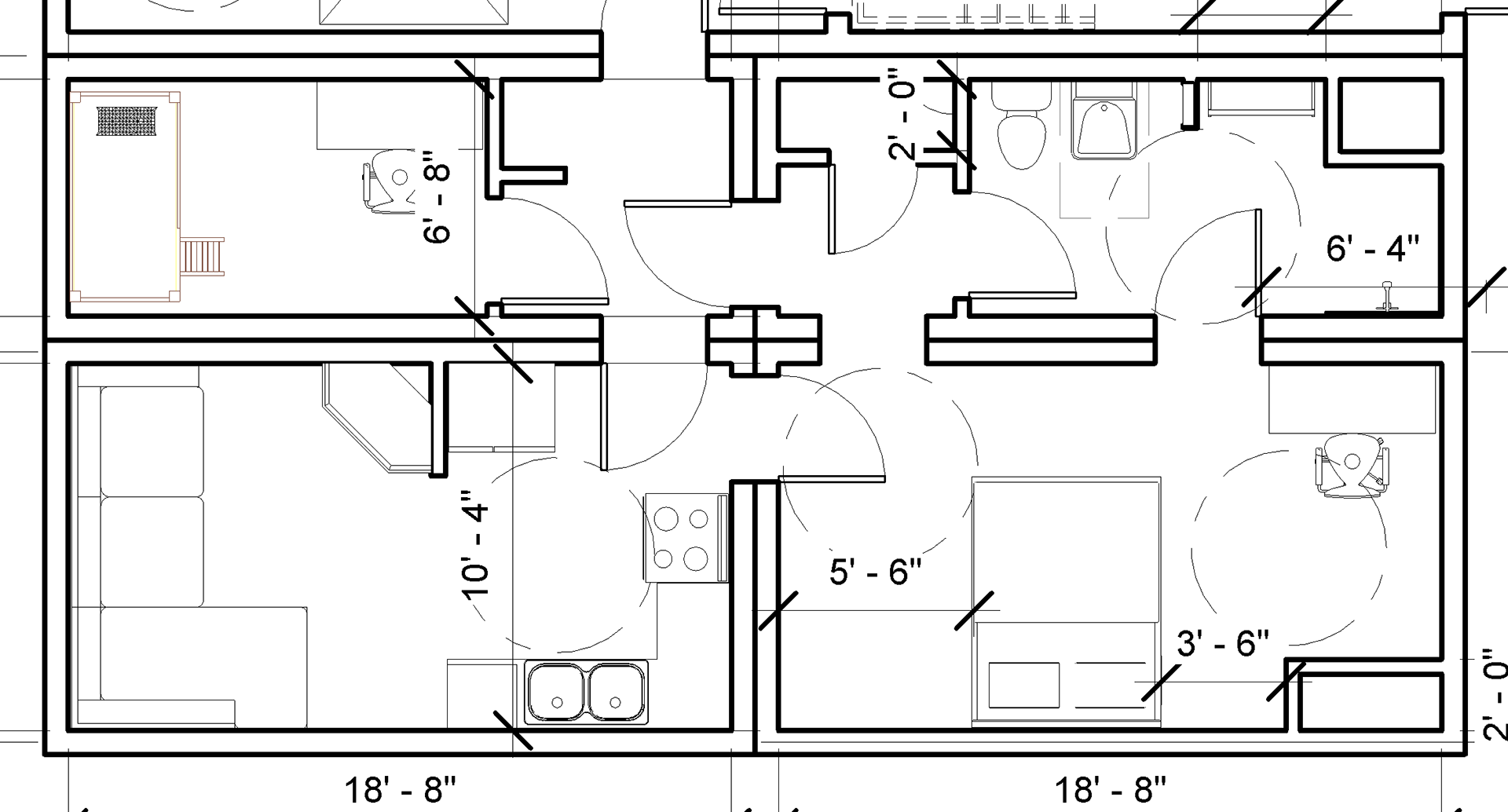
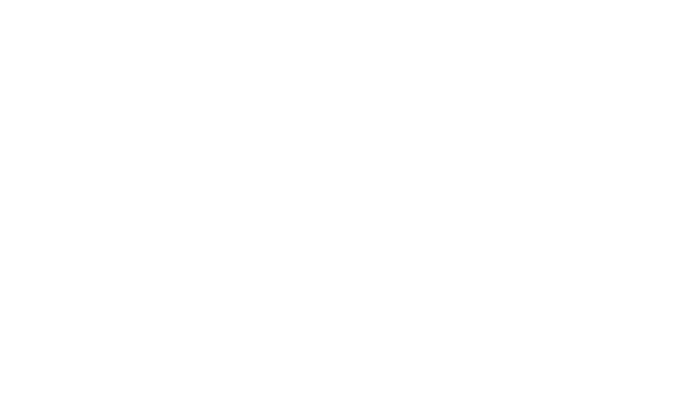
COST STUDY
Our units are significantly cheaper as compared to traditionally built affordable housing, as shown by the chart below. Values for our per-unit cost were estimated through a detailed cost breakdown included below.
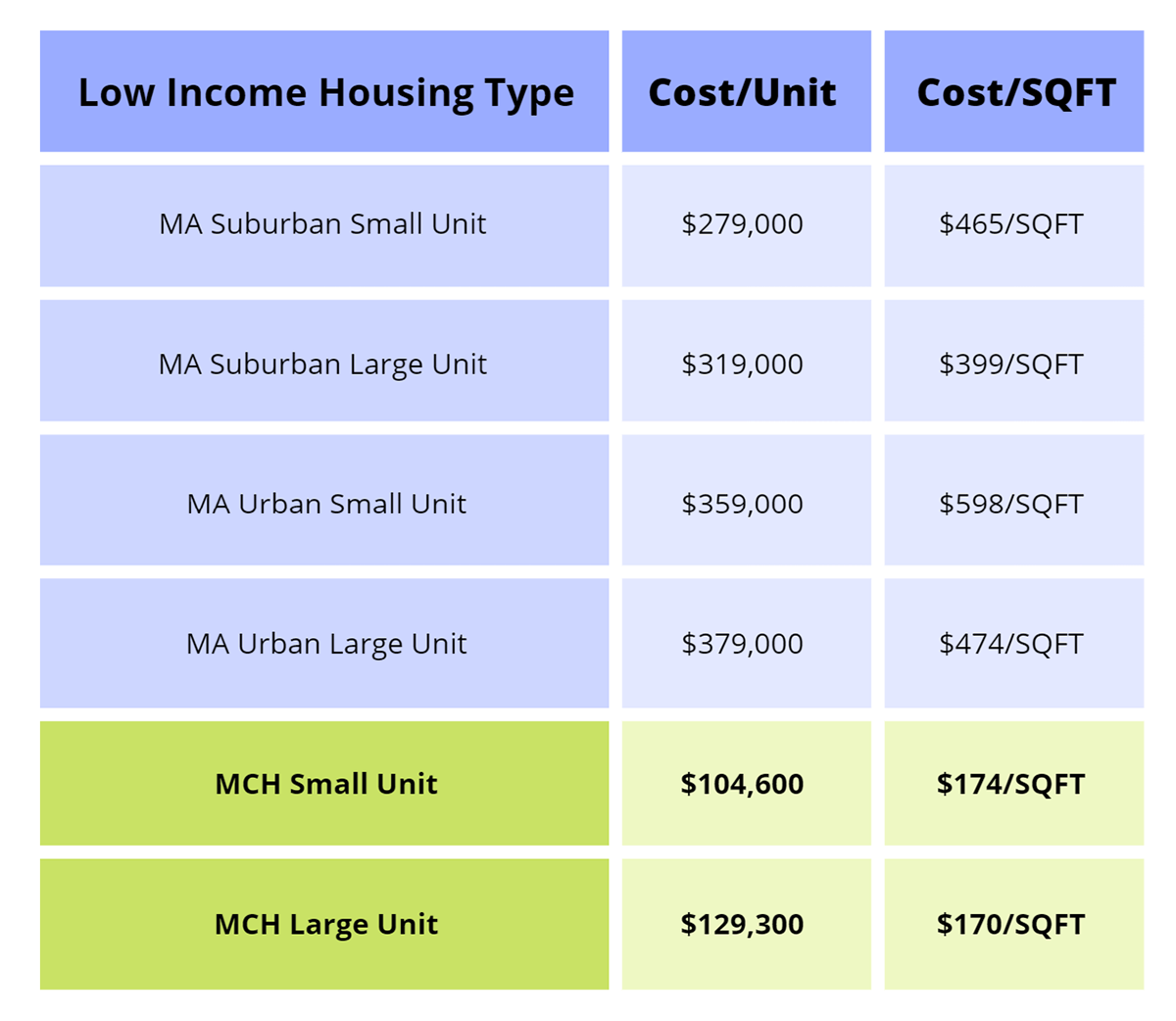
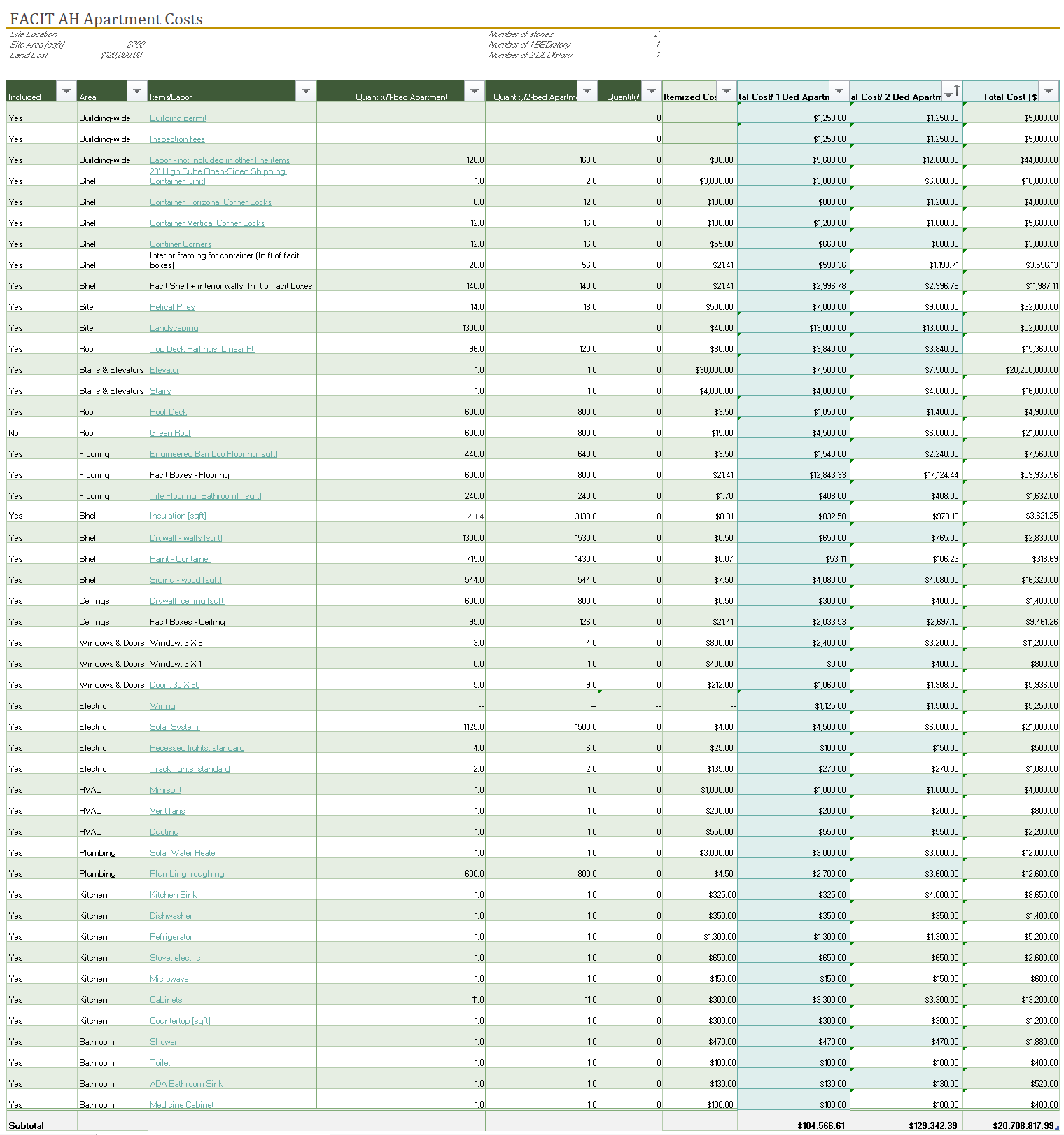
FUTURE
Prior to completing this research and design project, we plan to reach out to Facit Homes as well as the City of Boston (within which we have a personal connection) to propose MCH as a pilot project. Our hope is that Facit will be willing to aid our design and fabrication efforts using their prior experience using it for suburban single-family homes, and the City of Boston's Housing Innovation team will be able to partially fund and provide land and support for this pilot.